The blown film extrusion process is a widely used manufacturing technique in the plastics industry, particularly for producing plastic films. This method is essential for creating packaging materials, shopping bags, food wraps, and various other products that require a flexible, thin film. The process is efficient and versatile, allowing for the production of films in a range of thicknesses and materials, including polyethylene, polypropylene, and other thermoplastics.
Understanding the Blown Film Extruder Process
The blown film extruder process begins with the raw plastic material, typically in the form of pellets. These pellets are fed into the extruder’s hopper, where they are gradually moved towards the extruder barrel by a screw mechanism. As the pellets advance, they are heated to a molten state by the extruder’s heating elements. The screw inside the barrel mixes and pressurizes the molten plastic, ensuring uniform temperature and consistency.
Once the plastic is sufficiently melted and homogenized, it is forced through a circular die at the end of the extruder. The die’s design is crucial as it determines the initial shape and thickness of the film. As the molten plastic exits the die, it is inflated like a balloon by blowing air into it through the center of the die. This action causes the plastic tube, known as a “bubble,” to expand radially, creating a larger surface area.
The bubble is then cooled by a combination of air rings and fans that blow cool air onto the film. This rapid cooling process solidifies the plastic, allowing it to maintain its expanded shape. The bubble continues to rise, and as it does, it is gradually collapsed by a series of rollers. These rollers flatten the bubble into a double-layered film, which is then wound onto a roll for further processing or direct use.
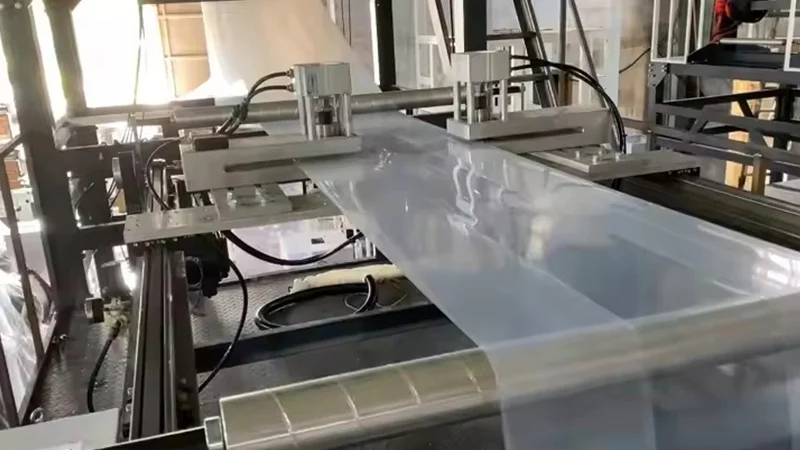
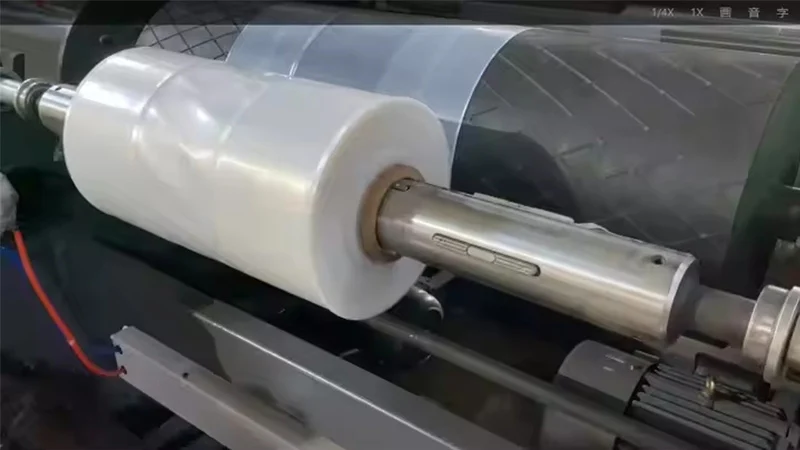
Key Components of a Blown Film Line
Several components are integral to the blown film extrusion process:
- Extruder Screw: The heart of the extruder, it melts and mixes the plastic pellets.
- Die: Shapes the molten plastic into a continuous tube.
- Blowing Air: Inflates the tube to create the bubble.
- Cooling System: Solidifies the plastic bubble into a film.
- Collapsing Frame and Wind-up System: Flatten and collect the film.

Advantages of Blown Film Extrusion
Blown film extrusion offers several advantages:
- Versatility: It can produce films from a variety of polymers and in various thicknesses.
- Strength and Durability: The process creates films with good tensile strength and puncture resistance.
- Efficiency: It is a continuous process, allowing for high-speed production and reduced waste.
- Cost-Effective: The process is relatively inexpensive compared to other film production methods.
Applications of Blown Film
The applications of blown film are extensive and include:
- Packaging: Bags, wraps, and liners for food, retail, and industrial products.
- Agriculture: Greenhouse films, mulch films, and silage wraps.
- Medical: Sterile packaging and medical-grade films.
- Consumer Goods: Garbage bags, food storage bags, and other household items.
Conclusion
The blown film extruder process is a cornerstone of the plastics industry, providing a cost-effective and efficient method for producing high-quality plastic films. With its ability to handle a wide range of materials and thicknesses, it caters to the diverse needs of various industries. As technology advances, the process continues to evolve, offering even greater precision, consistency, and sustainability in the production of plastic films.
For more detailed information on blown film extrusion, visit our Blown Film Extrusion Guide.